4090Sharps
WKR
Case prep sucks, and trimming brass even more so.
I was recently looking for a way to speed up the case trimming process, already owning a traditional style Lyman and Forster trimmer, and having recently experimented with the Lee Quick Trim on 5.7x28. I've tried using a hand drill on the Lyman, Forster, and Lee, but was unimpressed. I'm shooting a lot of .223 lately, handling each small piece of brass individually gets tiring, especially when progressive press loading has made me lazy.
Nicer press-mounted trimmers like the Dillon RT 1500 are $400+ but you can put them on a progressive press and not have to handle every piece of brass. Meanwhile, dedicated power trimmers like the Giraud or Henderson are even more and require handling each piece of brass. Plus, the idea of buying something motorized (liable to fail) from a reloading company didn't really appeal to me.
Then I stumbled upon a YouTube video showing the Honey Badger cranking out .223 to 300 Blackout conversions in a single pass.
Sure looked a lot like my Bosch router I bought a couple years ago for some projects and had been sitting unused since their completion.... Turns out it was the same router, the Bosch 1617 EVS. It's a $90 attachment, a $20 shroud to hook up a vacuum, and a $20 end mill. Roughly the equivalent of what it would cost to replace my Forster case trim kit.
fastandfriendlybrass.com
Here's a picture of my test setup (that loose screw has since been tightened). Once I get the proper toolhead for my progressive, I'll be moving it over there.
I'm using the trimmer with a Lyman Pro trim die ($50) and although I'm not using a jack nut to get perfectly square case mouths, case OAL is still falling within .0005" all around the edges of the case mouth. I've only run 25 cases through, but am very pleased with the consistency and ease.
If you end up trying one of these out, pay close attention to the trim die instructions. Most trim dies are meant to stand alone as both the trim and size die to ensure the cases don't spin. However, Lyman seems to have a really tight die and recommends running your brass through a sizer first. I overlooked this recommendation and got three cases stuck in the die before I figured out that I'm an idiot who needs to read the instructions.
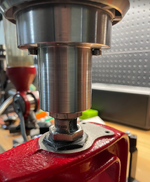
I was recently looking for a way to speed up the case trimming process, already owning a traditional style Lyman and Forster trimmer, and having recently experimented with the Lee Quick Trim on 5.7x28. I've tried using a hand drill on the Lyman, Forster, and Lee, but was unimpressed. I'm shooting a lot of .223 lately, handling each small piece of brass individually gets tiring, especially when progressive press loading has made me lazy.
Nicer press-mounted trimmers like the Dillon RT 1500 are $400+ but you can put them on a progressive press and not have to handle every piece of brass. Meanwhile, dedicated power trimmers like the Giraud or Henderson are even more and require handling each piece of brass. Plus, the idea of buying something motorized (liable to fail) from a reloading company didn't really appeal to me.
Then I stumbled upon a YouTube video showing the Honey Badger cranking out .223 to 300 Blackout conversions in a single pass.
Sure looked a lot like my Bosch router I bought a couple years ago for some projects and had been sitting unused since their completion.... Turns out it was the same router, the Bosch 1617 EVS. It's a $90 attachment, a $20 shroud to hook up a vacuum, and a $20 end mill. Roughly the equivalent of what it would cost to replace my Forster case trim kit.

Honey Badger Trimmer Adapter - Fast and Friendly Brass LLC
The original, and still the best, case trimmer for high speed/volume trimming. The Honey Badger adapts all standard trim dies to a Bosch 1617EVS router.

Here's a picture of my test setup (that loose screw has since been tightened). Once I get the proper toolhead for my progressive, I'll be moving it over there.
I'm using the trimmer with a Lyman Pro trim die ($50) and although I'm not using a jack nut to get perfectly square case mouths, case OAL is still falling within .0005" all around the edges of the case mouth. I've only run 25 cases through, but am very pleased with the consistency and ease.
If you end up trying one of these out, pay close attention to the trim die instructions. Most trim dies are meant to stand alone as both the trim and size die to ensure the cases don't spin. However, Lyman seems to have a really tight die and recommends running your brass through a sizer first. I overlooked this recommendation and got three cases stuck in the die before I figured out that I'm an idiot who needs to read the instructions.
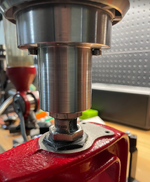