ResearchinStuff
WKR
This is the start to finish process I use on my tikka factory stocks to help them have a consistent POI and improve shootability. None of this is completely new information, but there are a few unique things I do, and this is a consolidation post.
This is stuff that I'm capable of doing to my personal possessions - if you try this and mess up your own stuff, that is on you. Step 1 is basically fool proof, even if you quit halfway through the stock will still function. The rest of the steps, once you start, your stock will not function until the step is finished.
Step 1: Free Float
Step 2: Install Pillars
Step 3: Bed action and lug
Step 4: Create negative drop at heel, negative comb angle, and flatten the bottom of the butt stock.
If you want to debate whether any of this is necessary, take it up with Patches, he handles my complaint hotline:
Anyhow, back to the stocks.
1. Free floating - this prevents barrel contact and POI changes when used in various positions and on various rests. I use a combination of the dremel tool with a sanding wheel to nock down the pressure points, and sand paper wrapped around deep drive sockets to open up the barrel channel. You really can't have too much clearance.
factory pressure ridges:
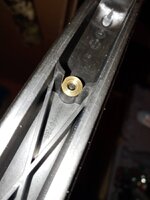
fixed:
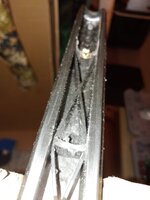
Floated, this booklet is about 1/16" thick.
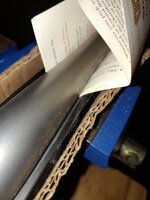
This is stuff that I'm capable of doing to my personal possessions - if you try this and mess up your own stuff, that is on you. Step 1 is basically fool proof, even if you quit halfway through the stock will still function. The rest of the steps, once you start, your stock will not function until the step is finished.
Step 1: Free Float
Step 2: Install Pillars
Step 3: Bed action and lug
Step 4: Create negative drop at heel, negative comb angle, and flatten the bottom of the butt stock.
If you want to debate whether any of this is necessary, take it up with Patches, he handles my complaint hotline:
Anyhow, back to the stocks.
1. Free floating - this prevents barrel contact and POI changes when used in various positions and on various rests. I use a combination of the dremel tool with a sanding wheel to nock down the pressure points, and sand paper wrapped around deep drive sockets to open up the barrel channel. You really can't have too much clearance.
factory pressure ridges:
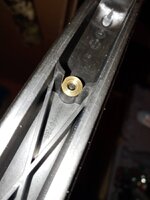
fixed:
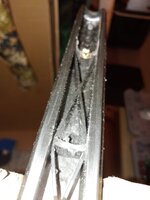
Floated, this booklet is about 1/16" thick.
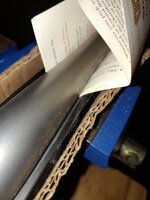