So, I thought I would share some DIY carbon fiber stock work I've been messing around with. No prior experience working with carbon fiber and resins, so much has been done through trying and failing. And it is kinda fascinating how "low-tech" one can work this high-tech material, with basic hand tools you'll find in the garage.
My primary motivation for doing this was the lack of good after market stocks meeting my requirements. Making my own stock I aimed at combining all the treats from diffirent rifle stocks I liked. Well that was the theory atleast...
The method I'm using is to first shape a high density foam core, and then wrap it with multiple layers of carbon fiber cloth, building the outer shell. For the first rifle stock I made, I wrapped the carbon fiber around the foam core and let the resin "air dry". It worked out OK, but it wasn't optimal. So for the second build I added a vacuum sealer to the mix.
The basic tools used: polyutherane/pvc foam, carbon fiber cloth, resin, knife, scissors (carbon fiber cloth really dulls them fast), wood file and sanding papers. I later added the vacuum sealer machine, breather cloth and peel ply:
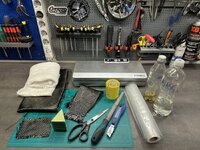
In order to get the necessary thickness (and to improve stiffness) I cut out carbon fiber cloth matching size of the foam and then stacked the polyurethane foam plates and sandwiched them with carbon fiber wetted with resin.
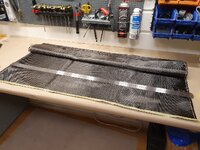
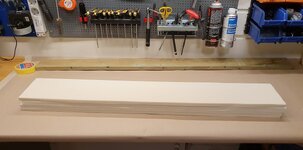
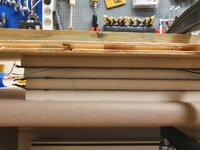
For maximum bonding it was wedged between some stiff boards and clamped down and left over night:
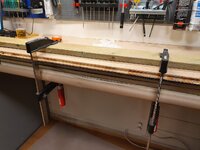
Once the sandwiched core was done I started to shape it according to the sketch. The stock was supposed to be "ergonomic", and a hybrid adapted for both off-hand competition shooting and hunting... (The mk1 turned out way too bulky):
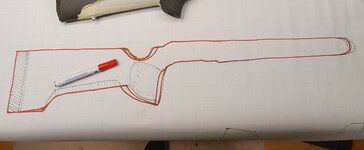
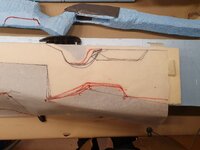
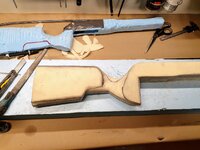
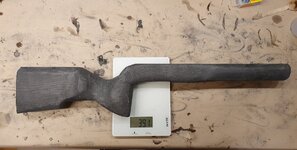
13.8 oz, so its pretty light. However, I screwed up while bedding the action/chassis in this one, and at the same time I realized that the ergonomics wasn't quite there yet. So back to start...
My primary motivation for doing this was the lack of good after market stocks meeting my requirements. Making my own stock I aimed at combining all the treats from diffirent rifle stocks I liked. Well that was the theory atleast...
The method I'm using is to first shape a high density foam core, and then wrap it with multiple layers of carbon fiber cloth, building the outer shell. For the first rifle stock I made, I wrapped the carbon fiber around the foam core and let the resin "air dry". It worked out OK, but it wasn't optimal. So for the second build I added a vacuum sealer to the mix.
The basic tools used: polyutherane/pvc foam, carbon fiber cloth, resin, knife, scissors (carbon fiber cloth really dulls them fast), wood file and sanding papers. I later added the vacuum sealer machine, breather cloth and peel ply:
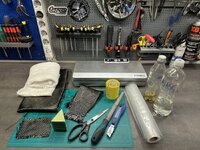
In order to get the necessary thickness (and to improve stiffness) I cut out carbon fiber cloth matching size of the foam and then stacked the polyurethane foam plates and sandwiched them with carbon fiber wetted with resin.
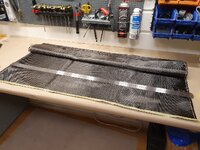
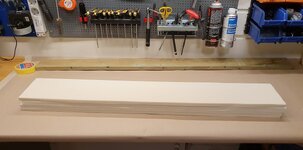
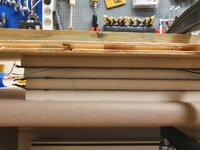
For maximum bonding it was wedged between some stiff boards and clamped down and left over night:
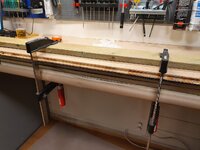
Once the sandwiched core was done I started to shape it according to the sketch. The stock was supposed to be "ergonomic", and a hybrid adapted for both off-hand competition shooting and hunting... (The mk1 turned out way too bulky):
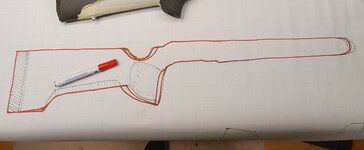
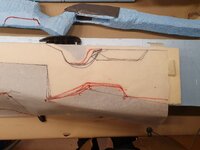
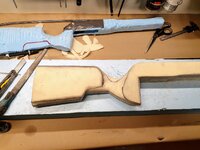
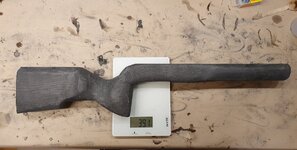
13.8 oz, so its pretty light. However, I screwed up while bedding the action/chassis in this one, and at the same time I realized that the ergonomics wasn't quite there yet. So back to start...
Last edited: