This project has been in the works for about 7 months now. It all started while my wife was browsing Pinterest and found some pretty cool epoxy river tables that someone was building and selling.
Now our current kitchen table is a $25 deal we found at goodwill, including 6 chairs. I sanding everything down, painted the chairs and coated and sealed the top but with 5 kiddos, it’s taken quite a bit of abuse and is starting to fall apart.
I started researching epoxy river tables and quickly learned some of them go for north of $10k. The more I looked into it though, I became convinced that with my nonexistent woodworking background, I could probably build one of these things.
First thing I did was went down to a local hardwood/lumber store and found a large slab of Myrtlewood which I figured would work great. It has some awesome splits and cracks which I thought would look awesome
After sanding the slabs, chipping away most of the dead pieces and sanding some more, I sealed the edges and with the help of my youngest boy, built the melamine forms and set it inside.
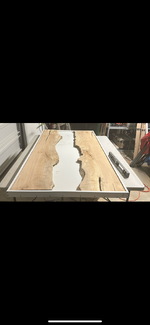
This is where the first problems started. I used tyvex tape on all the corners and edges, I went crazy with the tyvex tape to ensure the form didn’t leak but what I failed to do was use the Form Release spray that I had previously purchased and had sitting on a shelf 4’ away from the table. I later paid for that mistake with hours of routering and sanding when I went to remove the forms.
Gotta go pickup the boy from school but will try and continue this evening…
Now our current kitchen table is a $25 deal we found at goodwill, including 6 chairs. I sanding everything down, painted the chairs and coated and sealed the top but with 5 kiddos, it’s taken quite a bit of abuse and is starting to fall apart.
I started researching epoxy river tables and quickly learned some of them go for north of $10k. The more I looked into it though, I became convinced that with my nonexistent woodworking background, I could probably build one of these things.
First thing I did was went down to a local hardwood/lumber store and found a large slab of Myrtlewood which I figured would work great. It has some awesome splits and cracks which I thought would look awesome

After sanding the slabs, chipping away most of the dead pieces and sanding some more, I sealed the edges and with the help of my youngest boy, built the melamine forms and set it inside.
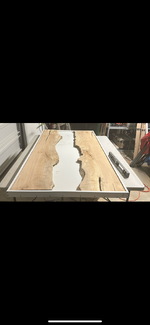
This is where the first problems started. I used tyvex tape on all the corners and edges, I went crazy with the tyvex tape to ensure the form didn’t leak but what I failed to do was use the Form Release spray that I had previously purchased and had sitting on a shelf 4’ away from the table. I later paid for that mistake with hours of routering and sanding when I went to remove the forms.
Gotta go pickup the boy from school but will try and continue this evening…